Specialized developer of Single-phase Liquid Immersion Cooling Solutions
High-Performance Biodegradable, Non-Toxic, Non-Corrosive Dielectric Coolants
BitCool®
Dielectric Immersion Coolants designed specifically for ASIC based miners
- Supports all ASIC Crypto-mining devices
ElectroCool®
Dielectric Immersion Coolants for Semiconductors and Servers
- Server / CPU / GPU / SSD / DRAM
- Lasers / LEDs / RF Amplifiers / Tubes / Processors / RADAR
- Battery / Fuel Cell cooling for Power Generation (Solar / Wind / Conventional) in stationary electrical storage applications
AmpCool®
Dielectric Immersion Coolants for Batteries, Electric Motors and Hydraulics
- Electric motors & motor controllers
- Hydraulic power transmission and actuator systems
- Aquatic applications for pressure compensating, insulating, and lubrication
- Battery and Fuel Cell cooling in hybrid and electric vehicles
VoltCool®
High Voltage Dielectric Heat Transfer Fluids for use Power and Distribution
- Power & Distribution Transformers, Switch Gear, AC & DC feeder lines
- High Voltage Battery / Fuel Cell cooling in specialty and stationary electrical storage applications
Products for Protecting and Cleaning Electronic Equipment During and After Immersion
VoltCool® Additives
Highly Concentrated Transformer Oil Protection
- Power & Distribution Transformers, Switch Gear, AC & DC feeder lines
- Anti-oxidation and Corrosive Sulfur Stop Additives for use with hydrocarbon transformer oils
Dielectric Solvents
Safe and Effective Removal of Dielectric Fluids and Mineral Oils
- Fully dielectric solvents for use with all electronics and immersion cooling systems
The Challenge of Thermal Management
Heat dissipation is the limiting factor for electronics performance
New multi-core CPUs / GPUs / FPGAs / ASICs waste heat can now exceed >4000W per device.
Air cooling is extremely power inefficient – consuming 40% to 50% of total facility energy usage:
- 30 – 40% of power is consumed by air-conditioning, fans, and associated air-cooling and handlers
- 5% – 20% of the power used by the device’s onboard fans alone!
- Air-cooling is space inefficient and severely limits the facilities compute density
- More than 1/3 the space in data centers / mines are dedicated to or dictated by air cooling requirements
- Fans, Filters, Air Conditioners, Chillers, Duct Work, Compressors, etc.
The Air-cooling infrastructure can represent 50% or more of capital infrastructure costs.
Air-cooling represents up to 50% of total operational costs (power, maintenance & operational costs).
Noise Levels often exceed 89db with facility hot aisle temperatures exceeding 100F are not uncommon.
Not to mention all the operational issues related to maintaining air filters, humidity control, corrosive air-borne contaminants, and mechanical air-handling equipment, etc.
Comparing PUEs of Air and SLIC Solutions
Be sure to remove server fan power use from the denominator!
- PUE = Power Usage Effectiveness
- Server fans consume between 10-20% of the total device power
- To accurately compare a SLIC PUE with air cooling PUE you must recalculate your air-cooled PUE to account for removing the device fans out of IT load.
Important SLIC Concepts
Your electronics generate as much heat (measured in kWs) as they consume in electricity.
Effectively your devices are just expensive and highly efficient heating elements. All the power they consume is exhausted as heat to the outside environment, typically through noisy and power-hungry fans.
Air is not a good conductor of heat; in fact, it is an excellent insulator.
Think of your down jacket, it is filled with air which is what traps your body heat inside the jacket thereby insulating the warm you from the cold outside. The down in the jacket is only there to create the air gaps that maintain the volume of insulating air between you and the outside environment.
Liquids are generally excellent conductors of heat because of their density.
Unfortunately, while water is one of the very best heat transfer fluids, it has one very significant draw back for use electronics cooling – it is highly conductive of electricity!
Therefore, in order to use water to cool electronics you must spend a lot of time and money engineering the complex plumbing and interface systems, as well as the protective failure modes, to keep water and electronics separate.
In addition, water has a low boiling and high freezing point. Thus to be effective, you must add glycol, biocides, and other chemicals to water to stop it from boiling, freezing and to stop the constant growth of organic matter in the system that clogs the pipes, cold-plates, and radiators.
Dielectric Coolants from Engineered Fluids…
are biodegradable, non-toxic, non-corrosive and are both excellent conductors of heat and fully non-conductive (Dielectric = non-conductive of electricity) up to 60KV.
Learn About The Key Differences Between Single-phase and 2-phase Full Immersion Cooling
Full Immersion Cooling delivers tremendous benefits, both from a capital and expense perspective…If you choose the right systems approach and the right liquid dielectric coolant.
ElectroCool & BitCool Are Simply the Better Dielectric Coolants
Comparison with Mineral Oil
Mineral Oil is highly flammable and subject to hazardous material storage requirements
Mineral Oil is not guaranteed to meet any operational characteristics
Mineral oils are commodities made by many oil refineries. Their compatibility profiles differ widely from one brand to another, and operational characteristics differ from batch to batch. They are sold without any guarantee of critical dielectric characteristics.
Mineral Oil is toxic and a known carcinogen in humans
Mineral Oil is incompatible with some common semiconductors components and materials
This board was immersed in mineral oil for about 4mths. Material incompatibility caused swelling of rubber gasket material in the capacitors on this Nvidia Tesla K80 GPU. This swelling caused the boards to fail due to the capacitors breaking off the board.
Mineral Oil is not biodegradable and must be handled and disposed of as a toxic material under OSHA regulations and the EPA.
Mineral Oils are not processed to be used with electronic circuitry
Mineral oils undergo little if any processing after refining. Commonly used to make engine oils, they are not filtered or dried, they are not formulated for use as a dielectric or even tested for materials compatibility.
Comparison with 3M Fluorinated Compounds
Fluoroketones and fluoroethers affect the health of workers
Worker sensitivity to halogenated compounds has been reported, including exposure by both inhalation and physical contact.
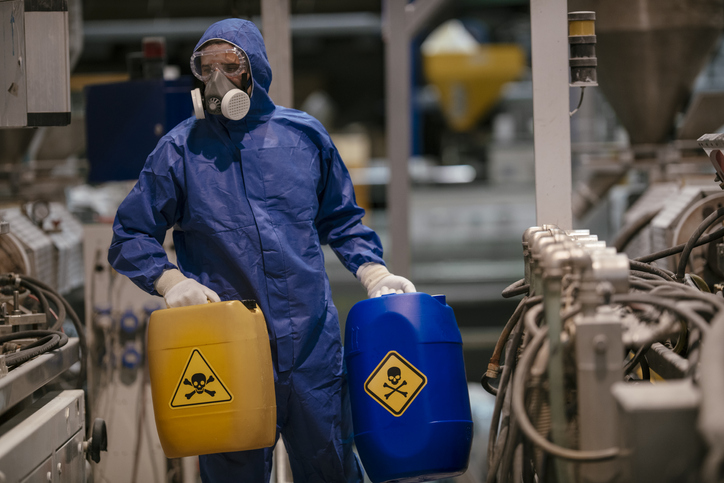
Fluorinated Fluids are very hygroscopic
Fluorinated fluids actively absorb water from their surroundings, particularly in humid environments, this absorption has two negative effects a) it reduces the dielectric strength of fluid, and b) the metal parts of the equipment rust.These rust particles will also breakoff during the boiling process and become suspended in the coolant.
Fluorinated fluids are not biodegradable and have very high Global Warming Potential (GWP)
Unlike ElectroCool and BitCool both with a GWP = 0, fluorinated ketones and ethers are not biodegradable. Atmospheric lifetimes for perfluorocarbon fluids range from 400 to 2000 years. The average GWP for Fluorinated fluids is >9,000 (according to ww.epa.gov)
Micro cavitation causes significant erosion of metals on cooled electronics
Violent boiling causes micro-cavitation and metal erosion at pin-socket connections and all exposed metals in the system. This causes metallic particle contamination of the coolant and dielectric breakdown of the two-phase coolant. The US Department of Defense concluded that metallic whisker formation was so excessive in fluorocarbon immersion cooling that it increased equipment failures by more than 60x.
Exposure to an electric arc creates toxic and hazardous substances
Exposure to an electric arcs creates HF (hydrogen fluoride) and PFIB (perfluorinatedisobutylene), both extremely hazardous, corrosive and toxic substances.
Fluorinated fluids are extremely heavy
Fluorinated fluids weigh twice as much as Engineered Fluids’ ElectroCool. The extra weight requires higher tank costs, floor loadings, and severely limits the applications.
(ElectroCool=6.84lbs/gal, Water =8.35lbs/gal, Fluorinert=14.02Lbs/gal)
2-Phase Immersion Cooling – 2PIC
Devices are fully immersed in low-temp boiling fluoroketone (halogenated fluids).
Cools the server through vaporization of fluid by hot electronics. Heat is removed by recondensing the vaporized coolant with gas-to-water heat exchangers, dumping waste heat using fluid-to-fluid or fluid-to-air heat exchangers. Requires water cooling infrastructure to the rack, vapor containment, and pressurized sealed system.
- Requires chilled water plumbed into each tank for the vapor to be cooled through a gas to fluid condenser.
- Fluid is vaporized by the heat of the electronics. Closed system is required to prevent the coolant from dispersing and evaporating.
- The boiling action of the coolant creates micro-cavitation which erodes the heated metals in the device destroying them and contaminating the coolant with metallic particles making the coolant fully conductive.
Challenges of 2-Phase Immersion Cooling
Applications using of 3M Fluorinated Compounds
Operationally Complex
- Fully sealed and pressurized systems are required to eliminate coolant lost and maintain safe operating environment. Custom solution is required per board similar to cold plates.
- Open bath systems contaminate the work environment with toxic vapors and require extensive vapor containment and exhaust systems. Coolant lost requires containment with complex material handling requirements are needed to ensure worker safety.
- Requires water cooling infrastructure in the data room.
Reduced Reliability due to Materials Incompatibility and Micro-Cavitation
The micro-cavitation caused by the boiling of the fluid against the metallic components causes these metals to be eroded away causing micro-particle contamination that degrades the dielectric strength of the coolant. This causes catastrophic failure of the electronics due to arcing and grounding if the coolant is not replaced regularly.
Very Costly
Constant coolant replenishment is required as coolant loss is excessive due to very low vapor pressure. 3M Novec coolants are very expensive (>$300 – $400/gallon)
Significant Environmental and Employee Safety Issues
Environmentally unfriendly (toxicity, non-biodegradable, high Global Warming Potential)
High risk due to handling and exposure due to vaporization and inhalation issues.
Water Cooling using Cold Plates
AKA – “Direct-to-Chip” / “Fluid-to-Chip” / “Water-to-Chip” / “Spot-Cooling”
Indirect cooling of devices through the use of chip-specific, fluid-cooled heat exchangers mounted on each chip.
Cools the chips through closed loop circulation of high pressure water through cold plates, dumping waste heat using fluid-to-fluid, fluid-to-air heat exchangers. Requires water cooling infrastructure to the rack, internal server plumbing, CRAC units, and fans.
Every board & chip layout requires a custom plumbing and cold plate design.
Cold plates are micro-filters and fail due to fouling from bio slime other contaminants.
Incoming water manifold pressures can exceed 200psi, requiring water plumbing rated at 1000psi per ASHRE.
Requires very expensive dripless connectors to prevent high pressure water failure and intrusion.
Challenges of Cooling Electronics with Water
Water Cooled Solutions generally…
Requires extensive water transport pipes and manifolds into the data room
Costs related to 5X pressure overdesign of water transport required by ASHRAE Standards
Operational problems including system clogging from biofilms and contaminates as well as water filters and water use
Having water in the data room can increase insurance costs due to catastrophic failure potential
Cold Plates particularly…
Requires a custom developed cold-plate design and plumbing for every chip and every board.
High manifold pressure (often >500psi at the manifold on the rack!) is required to force water through serial layout of microchannel cold plates.
Clogging of micro-channels has a massive and serial impact on system level cooling by Cold-plates.
“Point Cooling” – Cold plates only cool individual chips, the system still relies on air cooling for overall board cooling.
Inefficient due to thermal resistance (chip/paste/heat spreader/paste/Al block/water), results in 25-40% thermal transfer losses due to thermal resistance, which results in higher water flow requirements.
System still relies on air cooling, fans and now high pressure water pumps!
Increase failure rates of complex systems and general increase in electrical use and PUE of system
Back Door Radiators in particular…
Still requires hot and cold aisles and associate wasted space
System still relies on air cooling, extra fans and pumps actually raises PUE of system
BitCool® Industries and Applications
Single-phase Immersion with BitCool Dielectric Coolant Eliminates Complexity and Cost
- Eliminates all water in the data room and the associated catastrophic failure scenarios
- Silent and simple – no CRAC, no fans, no vibration, no air filters, no airborne contaminants
- Lower costs – significantly reduced capital and operational costs
- Elimination of all internal air-cooling infrastructure.
- Only requires a 5 -10C input and output temperature delta to provide highly efficient cooling
- Can use inexpensive passive heat dumps in the form of dry-coolers, or utilize standard active chilled water systems
- Eliminate or repurpose the physical space required for obsolete air-cooling infrastructure
- Highly efficient – up to 50% lower power requirements to cool the data center
- Repurpose cooling power to billable CPU power!
BitCool Coolants are highly effective, safe, and improves reliability
1600x more thermally efficient than air.
Biodegradable, non-allergenic, non-toxic.
No vapors or smell in the workplace, no respiratory or skin irritations or allergic reactions.
- Not flammable per OSHA
- Zero Global Warming Potential in use and manufacturing
- Increases reliability and the service life of device and electronic components
- Reduces Failure Mechanisms of corrosion, vibration, thermal expansion cycling, maintains constant temperature, no airborne contaminants, eliminates failures due to zinc and tin whisker growth.
BitCool® Dielectric Coolants for ASIC Miners
BitCool Dielectric Coolant is the highest performance biodegradable, non-toxic dielectric thermal management fluids available for specifically for ASIC Based mining devices
ElectroCool® Industries and Applications
High Performance Coolants for use in Electrical Applications
Aerospace
- Aeronautic and space instrumentation and radar cooling
Automotive & Robotics
- Electric motors & EM controller cooling & lubrication
- Battery cooling and thermal runaway suppression
- Kinetic Energy Recovery Systems (KERS) cooling and hydrostatic energy transfer
- Undersea pressure compensation and lubrication for submersibles
Power & Transmission Engineering
- Transformer Cooling
Semiconductor & Communications
- Electronics Immersion Cooling – CPU / GPU / FPGA / SSD and servers
- Amplifiers, Power Vacuum Tubes, & RF Transmitter cooling
- Optical & Laser Diodes cooling
ElectroCool® Dielectric Coolants for Servers / GPUs
ElectroCool Dielectric Coolants are the highest performance biodegradable, non-toxic dielectric thermal management fluids available.
ElectroCool Coolants feature the broadest material compatibility, highest safety, and widest useful temperature range.
ElectroCool® is the Green Alternative
From power savings to impact on the environment – ElectroCool wins!
ElectroCool power savings results in major reduction in greenhouse gases
Immersive fluid cooling using BitCool reduces power consumption by up to 45%
Assumptions:
- 2016 US EIA data for average annual emissions for electricity generation (a)
1kW/hr of electricity generation results in pounds of CO2 equal to:
An Air-cooled datacenter 10MW IT Load with 1.5 PUE equals a total power load of 15MW
24hr/d * 365d/yr * 15,000kW = 131,400,000 kW/hr annually of total power usage
(a) – US Energy Information Agency, https://www.eia.gov/tools/faqs/faq.php?id=74&t=11