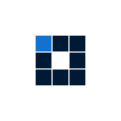
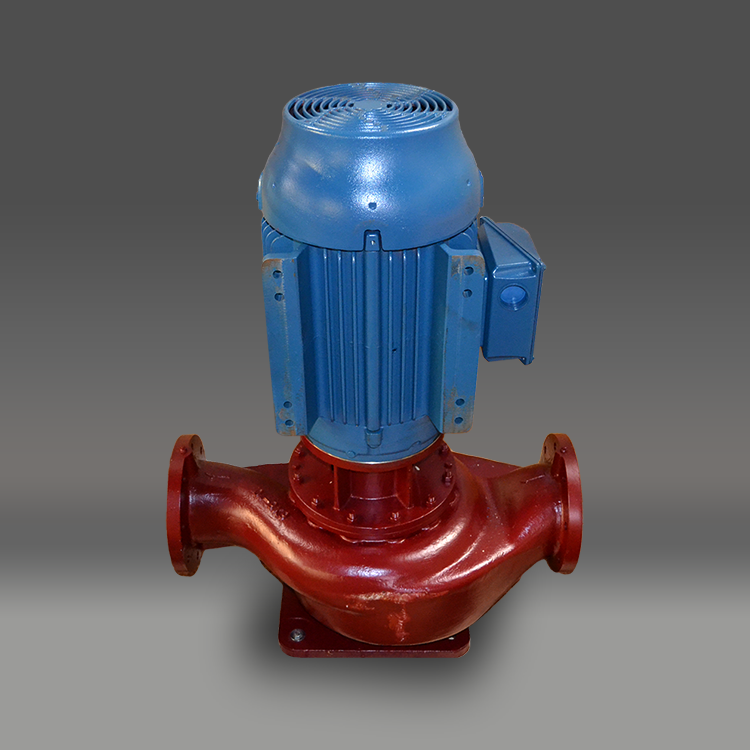
Pumps
Today’s pumps are both reliable by design, but when pumping our Dielectric Coolants they last even longer! How is this possible? It’s based on how pumps are constructed and in particular the seals used on the pump shafts that drive the pump. These seals are designed to be “water tight” and in the majority of SLIC systems we use carbon fiber / PTFE seals, these seals require lubrication to decrease wear. In water based systems, the water eventually displaces the lubricant allowing wear to occur, but in SLIC our dielectric coolants are in fact excellent lubricants allowing the pumps to operate on constant duty for often 1.5-3x longer than the expected operational life of the pump seal if it were operating with a glycol / water mix. In some systems we even immerse the electric motors directly in the Dielectric Coolant to both lubricate and cool the motor for further enhancement in MTBF of the pump.
Pumps we sell:
We offer pumps ranging in size from less than 1 hp to 50 hp. Our pumps are typically three phase but smaller pumps are offered in single phase. Many pumps can be combined with a variable speed option.
- 1 1/2hp Single Speed Centrifugal Pump – 115 / 230 VAC / 1 Phase / 60Hz
- 1 1/2hp Single Speed Centrifugal Pump – 230 / 460 VAC / 3 Phase / 60Hz
- 1 1/2hp Variable Speed Centrifugal Pump – 230 VAC / 3 Phase / 60Hz
- 1/2 hp Centrifugal Pump – 115/230 Volts, 1 Phase, 60 hz
- 1/2hp Single Speed Centrifugal Pump – 115 -230 VAC / 1 Phase / 60Hz
- 1/2hp Variable Speed Centrifugal Pump – 230 VAC / 1 Phase / 60Hz
- 1/3hp Single Speed Centrifugal Pump – 230 / 460 VAC / 3 Phase / 60 Hz
- 15hp Single Speed Centrifugal Pump – 230 VAC / 3 Phase / 60Hz
- 15hp Single Speed Centrifugal Pump – 460 VAC / 3 Phase / 60Hz
- 15hp Variable Speed Centrifugal Pump – 230 VAC / 3 Phase / 60Hz
- 15hp Variable Speed Centrifugal Pump – 460 VAC / 3 Phase / 60Hz
- 15hp Variable Speed Centrifugal Pump – 460 VAC / 3 Phase / 60Hz
- 1hp Single Speed Centrifugal Pump – 230 / 460 VAC / 3 Phase / 60Hz
- 1hp Single Speed Centrifugal Pump – 115-230 VAC / 1 Phase / 60Hz
- 1hp Single Speed Centrifugal Pump – 230-460 VAC / 3 Phase / 60Hz
- 1hp Variable Speed Centrifugal Pump – 230 VAC / 1 Phase / 60Hz
- 20hp Variable Speed Centrifugal Pump – 460 VAC / 3 Phase / 60Hz
- 25hp Single Speed Centrifugal Pump – 230 VAC / 3 Phase / 60Hz
- 25hp Single Speed Centrifugal Pump – 460 VAC / 3 Phase / 60Hz
- 25hp Variable Speed Centrifugal Pump – 230 VAC / 3 Phase / 60Hz
- 25hp Variable Speed Centrifugal Pump – 460 VAC / 3 Phase / 60Hz
- 2hp Variable Speed Centrifugal Pump – 230 VAC / 3 Phase / 60Hz
- 3/4 hp Single Speed Centrifugal Pump – 115 / 230 VAC / 1 Phase / 60Hz
- 3/4 hp Single Speed Centrifugal Pump – 115 / 230 VAC / 1 Phase / 60Hz
- 3/4 hp Single Speed Centrifugal Pump – 230 / 460 VAC / 3 Phase / 60Hz
- 3/4 hp Single Speed Centrifugal Pump – 230 / 460 VAC / 3 Phase / 60Hz
- 3/4hp Variable Speed Centrifugal Pump – 230 VAC / 1 Phase / 60Hz
- 30hp Single Speed Centrifugal Pump – 230 VAC / 3 Phase / 60Hz
- 30hp Single Speed Centrifugal Pump – 460 VAC / 3 Phase / 60Hz
- 30hp Variable Speed Centrifugal Pump – 230 VAC / 3 Phase / 60Hz
- 30hp Variable Speed Centrifugal Pump – 460 VAC / 3 Phase / 60Hz
- 3hp Single Speed Centrifugal Pump – 115 / 230 VAC / 1 Phase / 60Hz
- 3hp Single Speed Centrifugal Pump – 230-460 VAC / 3 Phase / 60Hz
- 3hp Variable Speed Centrifugal Pump – 400 VAC / 3 Phase / 50Hz
- 40hp Variable Speed Centrifugal Pump – 460 VAC / 3 Phase / 60Hz
- 50hp Variable Speed Centrifugal Pump – 460 VAC / 3 Phase / 60Hz
- 5hp Variable Speed Centrifugal Pump – 400 VAC / 3 Phase / 50Hz
- 7.5hp Single Speed Centrifugal Pump – 230 VAC / 3 Phase / 60Hz
- 7.5hp Single Speed Centrifugal Pump – 460 VAC / 3 Phase / 60Hz
- 7.5hp Variable Speed Centrifugal Pump – 230 VAC / 3 Phase / 60Hz
- 7.5hp Variable Speed Centrifugal Pump – 460 VAC / 3 Phase / 60Hz
Product Warranty
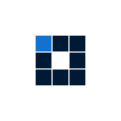
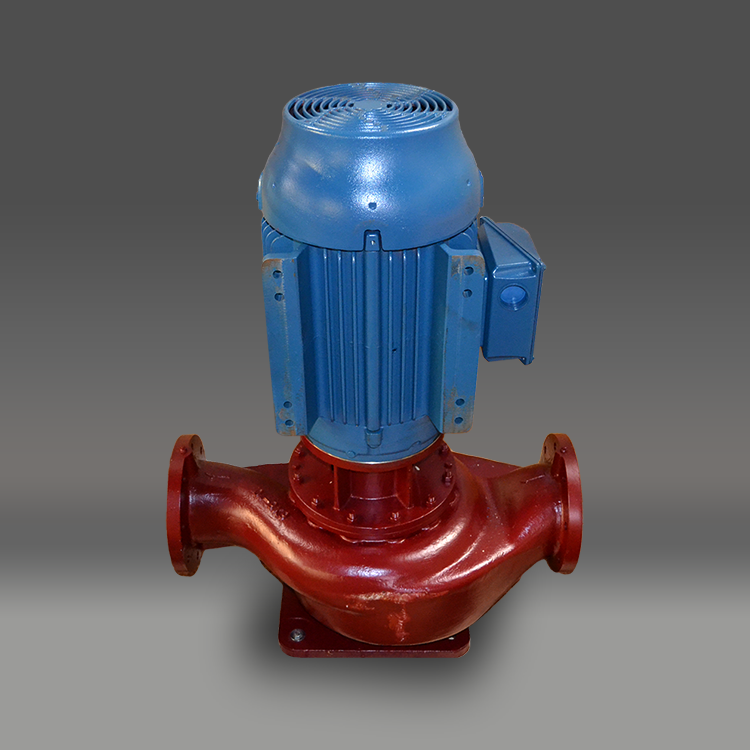
FAQs
What kinds of pumps should I use to circulate your Dielectric Coolants?
For circulating our Dielectric Coolants through a cooling system, we recommend the use of an appropriately sized centrifugal pump with Viton® seals (also called FKM). The pump and motor should be sized so that the desired flow rate and head is well within the efficiency curve of the pump/motor combination. Explosion-proof equipment is not required.
One problem that you may experience is that you want to get the slowest rotation speed possible with the largest impeller. This reduces the chance of cavitation within the pump and introduces the least number of bubbles into the mix. All of the pump manufacturers offer a pump sizing software or will size the pump for you given the Dielectric Coolant characteristics that you’ll be using. All of the required fluid information is available right on our product technical datasheets for each Dielectric Coolant..
Grundfos is our go to pump manufacturer. In particular we like their CR series of vertical centrifugal pumps.
Here is the
Grundfos Standard Product Finder.
Another vendor we use for large pumps is Bell and Gosset:
They have a pump sizing tool (called ESP Systemsyzer)
You can use almost any centrifugal or gear pump with Viton (FKM) seals for your system. If you are going to use a pump made out of a resin or plastic material just make sure to check the Material Compatibility Guide for the materials its made from to ensure its compatible with our Dielectric Coolants. Be sure to check out the materials used for the seals, impeller, and the pump chamber itself as most pumps will use a mix of materials in construction. Our coolants also provide excellent lubrication for steel, carbon fiber and ceramic bearings.
Many smaller 12v and 24v pumps used for Biodiesel, diesel, and fuel oil also work well with our Dielectric Coolants.
When using any pump sizing tool, make sure to pay close attention to fluid characteristics that the tool is set for as most use water as the base fluid. You can use water to get a close approximation, however, our Coolants have a higher viscosity which can result in the pump operating above its optimal efficiency range. So we recommend derating the pump by about 20% if all you can get is water curves for a pump. (100gpm = 80gpm).
Should I use cPVC, Copper, or Steel piping or something else for plumbing my SLIC system?
We definitely recommend that you use Schedule 80 Chlorinated PVC (cPVC) vs copper or steel. Do NOT use PVC, you must use Chlorinated PVC! There is a big difference, PVC will become brittle over time due to interaction with our Coolants and the heat.
Here is a quick comparison of the different materials:
PROs for cPVC
1. Very simple to cut and glue-up
2. Uses a simple glue-up process (you must use primer and then glue for all joints)
3. Easy to add new fittings anywhere required with saddles and cuts
4. There are more than 400+ fittings for cPVC. Make sure to get all fittings and valves with Viton/FKM gaskets and O-Rings.
5. cPVC is far cheaper that other options in both raw materials and cost to install
6. cPVC is rated up to 100C operating temperature – watch your pressure de-rating based on operating temp!
7. cPVC is electrically non-conductive
8. You can use Teflon Tape to seal threaded joints
CONs for cPVC
1. Operating temperature is limited based on pressure required and not more than 100C
2. Most cPVC fittings intended for use with water will use Buna O-rings and gaskets. You cannot use Buna with our Coolants, they will swell and your system will fail! You must use only Viton/FKM fittings with our Coolants. Almost all fittings are available in both Buna and FKM – so be sure you get FKM
3. Most flow limiting valves that rely on a floating ball will not work because the density of coolant is less water so the valve balls will not float in our Coolants. Make sure to do a test of the balls to ensure they will float in our Coolant before using them.
4. cPVC fittings cannot be removed once they are glued-on, if a fitting is not correctly glued up or it leaks you must cut out the bad joint and replace the fitting and pipe.
5. Please ensure you have good ventilation during the glue-up process as the glue and primer.
PROs for Copper and Steel
1. Higher pressure rating and not de-rated by temperature
2. Can easily be disconnected and reconnected and patched at a joint (make sure to clean off all the coolant or you will have a lot of smoke during the soldering)
3. You can use Teflon Tape or Hydraulic PTFE paste to seal threaded joints
CONs for Copper
1. Expensive
2. Requires extensive soldering expertise to get clean sealed joints
3. Conducts electricity – this is particularly bad with steel or aluminum tanks because if the device shorts to the tank it can be practically impossible to track down a short, and it can create a shock hazard across the entire system.
4. Most cPVC fittings intended for use with water will use Buna o-rings and gaskets. You cannot use Buna with our Coolants, they will swell and your system will fail! You must use only Viton/FKM fittings with our Coolants. Almost all fittings are available in both Buna and FKM – so be sure you get FKM
5. Most flow limiting valves that rely on a floating ball will not work because the density of coolant is less water so the valve balls will not float in our Coolants. Make sure to do a test of the balls to ensure they will float in our Coolant before using them.
6. Limited number of fittings, and copper fittings are all Buna seals, you must use Viton/FMK for gaskets and O-Rings.
5. Requires the use of open flame to solder and assemble
CONs for Steel
1. Conducts electricity – this is particularly bad with steel or aluminum tanks because if the device shorts to the tank it can be practically impossible to track down a short, and it can create a shock hazard across the entire system.
2. Use of steel requires complex jointing with threads or grooved pipe (Victaulic) type joints, these are expensive and require significant expertise execute. Also they are typically designed for significant pressure ratings which is typically not necessary with a SLIC system.
3. Steel is heavy and requires lots of equipment and manpower to set up.
4. Limited number of fittings, and copper fittings are all Buna seals, you must use Viton/FKM for gaskets and O-Rings
5. Most flow limiting valves that rely on a floating ball will not work because the density of coolant is less water so the valve balls will not float in our Coolants. Make sure to do a test of the balls to ensure they will float in our Coolant before using them.
What pumps are compatible with BitCool and ElectroCool?
The good news is that you can use just about any centrifugal pump that has FMK / Viton O-Rings, this means that you do not have to use specialty chemical pumps. Our Coolants are very pump friendly in terms of lubrication and materials and most centrifugal water pumps will work fine as long as they have the correct gasket and O-ring materials.
Because SLIC open tank systems do not generally need high pressure, but rather high volume, you’ll want to use the largest impeller possible and have that impeller turn as slow as possible (1800 RPM is a common rotational speed we like to use), this creates less cavitation and provides greater overall flow.
We’ve had great success with Grundfos CR and CRE pumps.vertical multi-stage centrifugal pumps.
Other pumps we use are Bell and Gossett pumps, and March pumps.
In almost all cases we use a VFD – variable frequency drive, which enables a 3phase pump to change rotational speed based on user input or temperature feedback. We like this feature as it allows us to dial in the pump speed and thus coolant flow based on the the temperature of the devices and the coolant return temperature
Product Warranty
Sustainability
We want to change the way the world cools all electronic devices and help our planet at the same time! We believe that we can reduce the energy demands and increase the performance of any electrical device that generates waste heat (which is all of them!).
Learn More