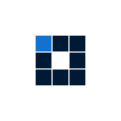
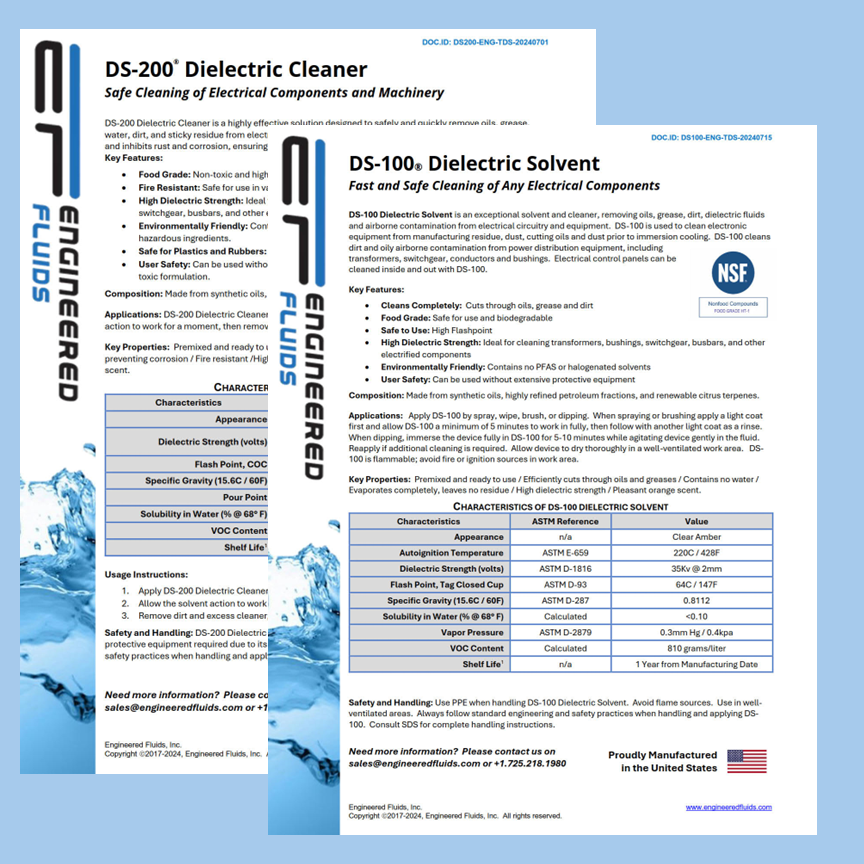
Dielectric Solvents and Cleaners
Engineered Fluids makes dielectric solvents used in maintenance of electrical and electronic equipment
DS-100 Dielectric Solvent is an exceptional solvent and cleaner, removing oils, grease, dirt, dielectric fluids and airborne contamination from electrical circuitry and equipment. DS-100 solvents are used to clean electronic equipment from manufacturing residue, dust, cutting oils and dust prior to immersion cooling. DS-100 cleans dirt and oily airborne contamination from power distribution equipment, including transformers, switchgear, conductors and bushings. Electrical control panels can be cleaned inside and out with DS-100.
DS-200 Dielectric Cleaner is a highly effective solution designed to safely and quickly remove oils, grease, water, dirt, and sticky residue from electrical components, machinery, motors, and tools. It displaces water and inhibits rust and corrosion, ensuring the longevity and reliability of your equipment. DS-200 leaves a protective, anti-rust and anti-corrosion layer on your equipment.
Engineered Fluids’ Dielectric Solvents do not contain any PFAS, halogenated solvents or other hazardous ingredients. They have a high dielectric strength, enabling them to be used safely on all types of electrical apparatus without the danger of electrical shorts or unintended arcing during operation. Engineered Fluids’ Dielectric Solvents removes fluid coolants, grease, dirt, pollution, oils and a wide variety of other materials.
Key Features:
- Cleans Completely: Cuts through oils, grease and dirt; displaces moisture
- Food Grade: Both Products are classified “Food Grade” in the US.
- Safe to Use: Readily biodegradable
- Safe to Use: High Flashpoint
- High Dielectric Strength: Ideal for cleaning transformers, bushings, switchgear
electrified components - Environmentally Friendly: Contains no PFAS or halogenated solvents
- User Safety: Can be used without extensive protective equipment
- Available in 4L, 20L, & 200L containers and 28 oz aerosol cans
How to Use DS-100:
- DS-100 is flammable so avoid fire or ignition sources in work area.
- Apply DS-100 by spray, wipe, brush, or dipping. When spraying or brushing heavily contaminated or dirty equipment, apply a light coat of DS-100 first and allow the product of 3-5 minutes to dissolve the dirt and oils, then follow with another light coat as a rinse
- When dipping, immerse the device fully in DS-100 for 10-15 seconds while agitating device (moving the device up and down) gently in the solvent
- Reapply if additional cleaning is required
- Allow device to dry thoroughly in a well-ventilated work area
How to Use DS-200:
- DS-200 is not classified as flammable per OSHA.
- DS-200 is applied via wiping, a brush or spray. DS-200 dissolves grease, dirt, pollution.
- DS-200 leaves a protective layer on equipment that repels water and prevents rust and corrosion. DS-200 also acts as a light lubricant.
Key Characteristics
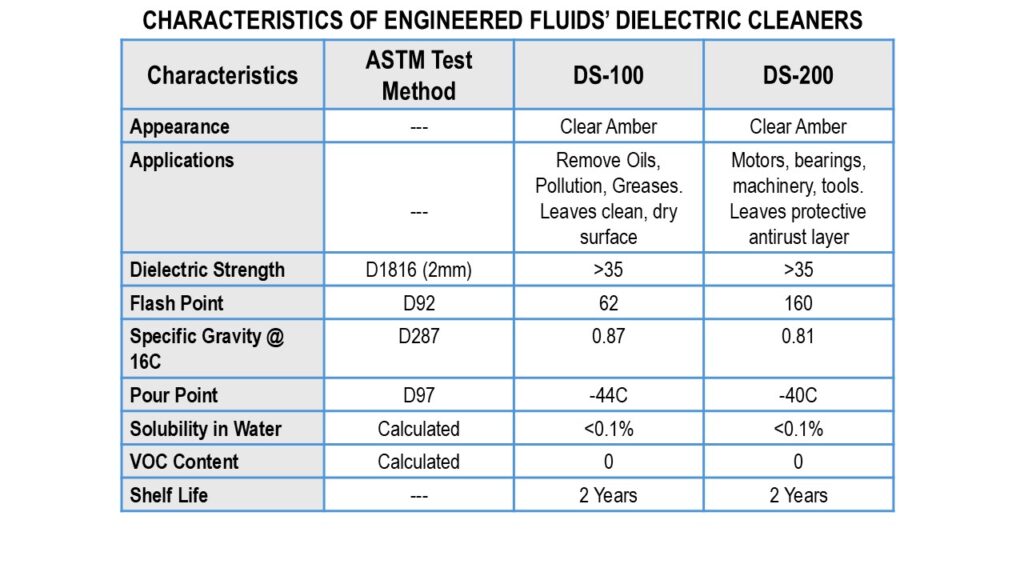
#image_title
Product Warranty
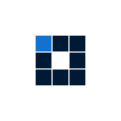
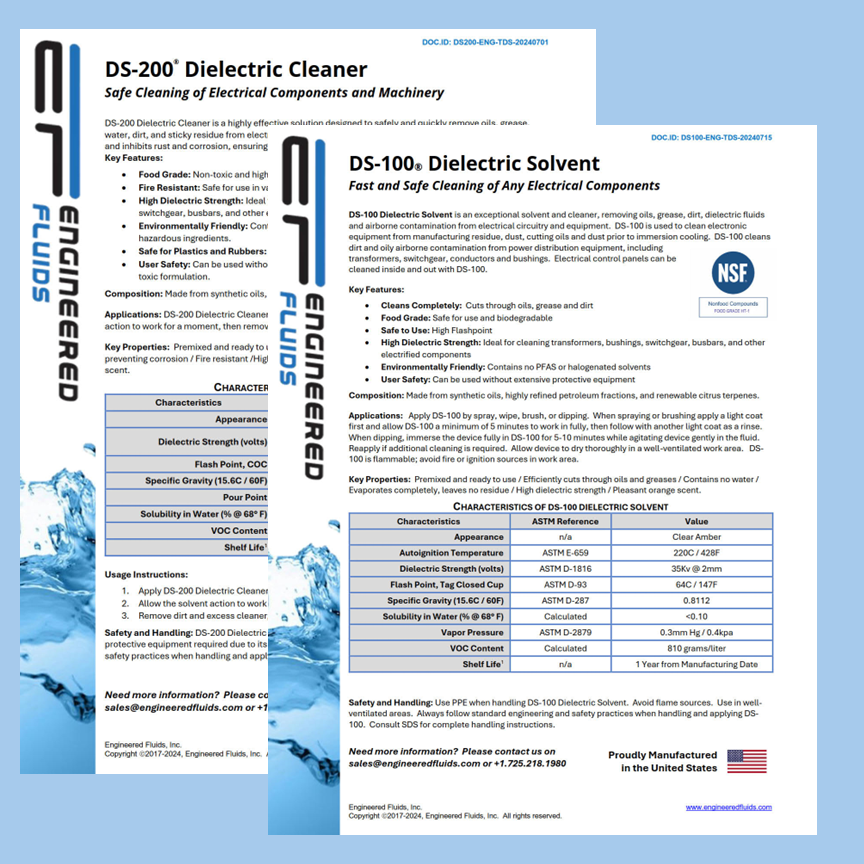
Product Resources
FAQs
Will DS-100 be the right product to help me clean electronic equipment like motherboards and components?
Our Dielectric Solvent DS-100 is specifically designed to clean electronics of manufacturing waxes, greases, dust and other contaminates. It is formulated to fully remove all of the Engineered Fluids’ Dielectric Coolants from electronics. If you are going to immerse your devices in our Dielectric Coolants after cleaning, then it is much better to use the Dielectric Coolant ( AmpCool , BitCool or ElectroCool ) as the cleaning solvent as you will will not have to wait for the DS-100 to dry off before immersing. By agitating your devices in the Dielectric Coolant the devices will be fully cleaned and ready for immersion. If you will be cleaning them to remove our Dielectric Coolants for use in air, or returning them to a vendor then you must use DS-100 to clean them.
DS-100 will fully remove all the dirt and greases from your electronics. You should use a parts washer to clean the electronics and then leave them in a well ventilated area to allow them to dry.
Product Warranty
Sustainability
We want to change the way the world cools all electronic devices and help our planet at the same time! We believe that we can reduce the energy demands and increase the performance of any electrical device that generates waste heat (which is all of them!).
Learn More